4 SECRETS TO SUCCESSFUL RESILIENCE BUILDING IN MANUFACTURING
Resilience was a business buzz word during the height of COVID, and it continues to be in today’s new normal.
With so much change and disruption happening in the world and across industry markets, being adaptable is critical. But what does it really take to make your manufacturing company truly resilient?
In the latest two-part episode of my Manufacturing Mastery podcast (Episodes 5 and 6), I sat down with Deidre Lewis, General Manager HSE Energy Markets at Origin Energy to discuss the energy market, and dig into what she sees as the crucial components of resilience building.
With over 25 years of varied operational experience in large Australian businesses, Deirdre has seen things done badly. However, she’s now in a position to make improvements and is passionate about building resiliency into organisations. Here are the key insights I took away from our discussion.
DON’T JUST LOOK AT PROCEDURE; LOOK AT HOW IT IS
To be resilient and succeed in today’s market, you need to be adaptable. However, to create adaptability, you can’t solely focus on procedures and systems. That’s because procedures and systems are written in a static environment – they don’t account for real-life variation.
To be adaptable, you need to instead look at work and situations as they’re happening in real-time. In other words, to look at how they are, rather than how you imagine them to be.
The reality is that people are making decisions all the time, and therefore resilience is built into the day-to-day, but often we don’t understand it. Our job as leaders is to unpick it and make sure we do understand it.
START CONVERSATIONS TO DRIVE ONENESS
To understand resilience in the day-to-day, we need to figure out how people make decisions and support them to find their own solutions. This process starts by opening the conversation. Ask your people how things are, rather than relying on how you think they are.
It’s amazing what people are willing to talk about if you create the right environment. They will often open up and share things they haven’t shared before. This can be a big learning journey and a real eye-opener.
When people start talking to you and to each other, it can also create a mutual appreciation and understanding between roles. This includes a revealing of the ugly truths, such as how constrained work is or how difficult it is to work under current conditions.
This openness can break down silos, uncover reality, and drive oneness or a sense of working togetherness that identifies issues and enables resilience, dynamism, and efficiency.
FOCUS ON WELLNESS NOT JUST WHAT WENT WRONG
People naturally want to fix things and do a good job. This makes them focus on what went wrong and finding a solution. However, it’s important you don’t just look at what’s going wrong or what failed in a reactive way. You also need to look at what’s going well in a proactive way.
This approach requires a shift in organisational thinking. When something goes wrong, it’s easy to measure it, for example, by the number of injuries or complaints. But when things are going right, there’s often no ready measure for improvement. How can you rethink this?
MOVE AWAY FROM BLAME TOWARDS SEEKING TRUTH
When things are going wrong or do go wrong, it’s often kept quiet. People naturally clam up as they don’t want to admit that they’ve made a mistake – whether the mistake was stopping the line or costing the business $10,000.
However, this natural tendency to cover up issues can be costly in itself. To avoid it, you need to create a culture where they won’t get blamed and feel comfortable raising issues. When you know the issues, you have the power to fix them.
This isn’t easy, but it starts with management. As well as instilling in staff that it’s okay to make mistakes and admit them, you also need to lead by example. When someone raises the undiscussable, leaders need to respond appropriately. This could mean breaking the initial news in private first, so they have time to work through initial back-lash reactions.
In addition, rather than carrying out an investigation, with one-on-one interviews, bring everyone together. Get the most senior leader to say no blame will be placed; that you just want to understand what’s going, so you can improve it. People can then work in groups to discuss, ask questions and become part of the solution – rather than being placed at fault.
Ultimately, it’s about creating a psychologically safe environment.
Resilience runs much deeper than surface level processes and procedures. It comes from putting people first, listening to them and learning from them. When people feel part of a bigger dynamic whole, the more they’re able to talk about what’s happening, work together, and respond more quickly to both threats and opportunities.
Are you ready to be the next success story?
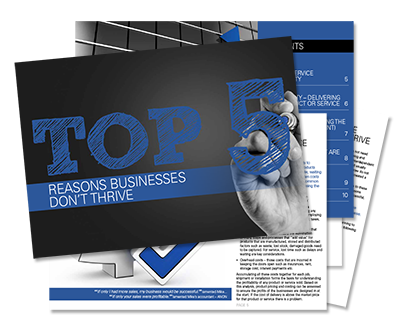
GETTING THE BASICS RIGHT
Pandemic or no pandemic - avoid the common traps that lead to business failure with this free e-book
Submit your details and you'll be given immediate access to download this FREE e-book.